Understanding Porosity in Welding: Exploring Reasons, Effects, and Avoidance Methods
Porosity in welding is a consistent challenge that can considerably impact the quality and integrity of welds. As experts in the welding sector are aware, understanding the causes, effects, and avoidance techniques associated with porosity is essential for achieving durable and dependable welds. By delving right into the origin of porosity, examining its damaging impacts on weld high quality, and discovering effective prevention strategies, welders can enhance their expertise and abilities to generate premium welds consistently. The detailed interplay of aspects contributing to porosity calls for an extensive understanding and a proactive technique to make certain effective welding results.
Typical Root Causes Of Porosity
Contamination, in the type of dust, oil, or corrosion on the welding surface area, creates gas pockets when heated, leading to porosity in the weld. Inappropriate securing takes place when the securing gas, generally made use of in procedures like MIG and TIG welding, is unable to completely shield the liquified weld pool from reacting with the surrounding air, resulting in gas entrapment and subsequent porosity. Furthermore, insufficient gas coverage, frequently due to wrong circulation prices or nozzle positioning, can leave components of the weld unprotected, allowing porosity to form.
Results on Weld High Quality
The presence of porosity in a weld can significantly jeopardize the overall high quality and integrity of the bonded joint. Porosity within a weld creates voids or cavities that compromise the structure, making it a lot more at risk to breaking, corrosion, and mechanical failure.
In addition, porosity can hinder the performance of non-destructive screening (NDT) techniques, making it testing to identify various other defects or gaps within the weld. This can bring about substantial safety and security problems, particularly in essential applications where the structural honesty of the bonded parts is critical.
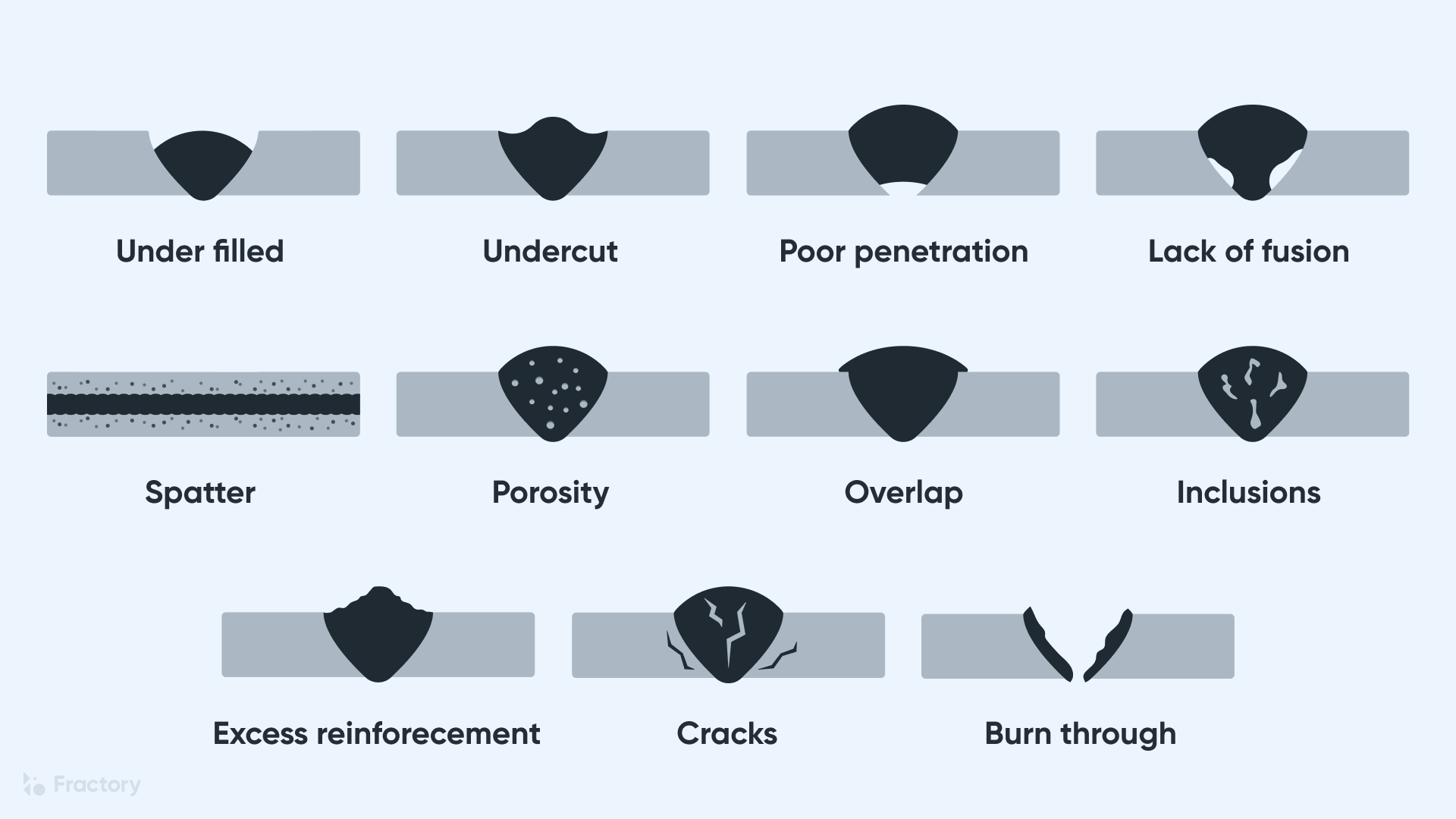
Prevention Techniques Summary
Provided the damaging influence of porosity on weld quality, effective avoidance methods are important to maintaining the structural integrity of welded joints. Additionally, picking the ideal welding specifications, such as voltage, existing, and travel speed, can aid lessen the threat of porosity development. By including these avoidance techniques redirected here into welding practices, the event of porosity can be substantially decreased, leading to stronger and extra trusted bonded joints.
Value of Proper Protecting
Proper shielding in welding plays a vital role in preventing atmospheric contamination and making sure the honesty of bonded joints. Shielding gases, such as argon, helium, or a mix of both, are frequently used to secure the weld pool from responding with aspects airborne like oxygen and nitrogen. When these reactive aspects enter into contact with the warm weld pool, they can create porosity, leading to weak welds with minimized mechanical properties.

Poor securing can lead to numerous issues like porosity, spatter, and oxidation, jeopardizing the architectural honesty of the bonded joint. Adhering to correct protecting practices is crucial to create premium welds with minimal flaws and guarantee the durability and integrity of the bonded components.
Surveillance and Control Techniques
Exactly how can welders effectively keep an eye on and manage the welding procedure to ensure ideal results and avoid issues like porosity? One secret approach is with making use of advanced tracking technologies. These can consist of real-time monitoring systems that supply responses on parameters such as voltage, present, travel rate, and gas flow rates. By continually checking these variables, welders can determine discrepancies from the ideal conditions and make prompt changes to avoid porosity formation.

Additionally, implementing appropriate training programs for welders is crucial for monitoring and managing the welding procedure successfully. What is Porosity. Informing welders on the value of preserving constant criteria, such as correct gas protecting and take a trip rate, can help protect against porosity problems. Normal evaluations and accreditations can also ensure that welders are efficient in surveillance and regulating welding processes
Additionally, using automated welding systems can enhance surveillance and control capabilities. These systems can exactly control welding parameters, minimizing the likelihood of human error and guaranteeing regular weld top quality. By incorporating advanced tracking innovations, training programs, and automated systems, welders can properly check and more helpful hints manage the welding procedure to reduce porosity problems and accomplish top quality welds.